Combining the Speed of Red X with the Optimization of Six Sigma
In today’s competitive manufacturing environment, efficiency and accuracy in solving problems can make the difference between success and failure. Red X® and Six Sigma are two methodologies that have earned their place in the problem-solving toolbox.
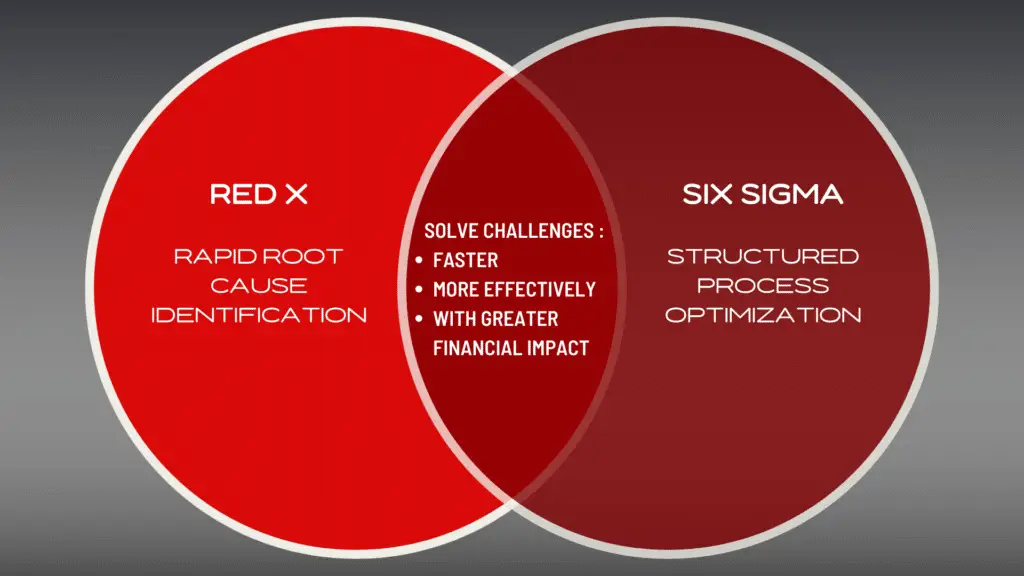
While often viewed as separate methods, their strengths are highly complementary. By combining the rapid root cause identification of Red X with the structured process optimization of Six Sigma, companies can tackle challenges faster, more effectively, and with greater financial impact.
To provide deeper insights into how these methodologies complement each other, we interviewed three experts certified in both Red X and Six Sigma: Esther Fondermann – a Six Sigma Master Black Belt and Red X Master, Jay Zhu – A Sig Sigma Black Belt and Red X Consultant, and Tom Smith – a Six Sigma Black Belt and Red X Consultant.
Together, they bring over 30 years of experience in the problem-solving space, working across multiple industries to tackle some of the most complex challenges in manufacturing. Their insights help illuminate how leveraging both tools can enhance problem-solving capabilities, improve efficiency, and deliver measurable results.
So, what is Six Sigma?
Six Sigma: Optimizing Processes Through Structure
Six Sigma is a structured, data-driven methodology aimed at reducing variation and improving process quality. Its name is derived from the goal to obtain six sigma (or standard deviations) from the mean of a process before having a defect. This would result in a defect rate of only 3.4 defects per million products. a standard that represents operational excellence.
It uses the DMAIC framework (Define, Measure, Analyze, Improve, Control) to guide projects from identifying a problem to implementing long-term solutions. Esther explains, “Six Sigma works best when factors are known, measurable, and ideally controllable.” Each phase of DMAIC plays a vital role:
• Define: Clearly identify the problem, objectives, and team.
• Measure: Analyze the current process and collect measurable data.
• Analyze: Apply tools like Regression Analysis to pinpoint key variables.
• Improve: Optimize those variables using methods such as DoE (Design of Experiments).
• Control: Standardize and document solutions to ensure sustainability.
Jay emphasizes the balance in DMAIC, noting, “These five stages form a closed loop for problem -solving, like FACTUAL [the Red X framework], but more balanced in work loading of each step.”
Tom emphasizes the use of DMAIC for variation reduction, noting, “These are the standard work stages to implement when executing a variation reduction project, … This is effective when processes are being initially developed or are drifting out of control when mature.”
While Six Sigma thrives in data-rich environments, it is less effective when hidden or unknown factors are at play. Tom warns, “Deploying Six Sigma as an investigative root cause analysis tool is a misuse of the methodology. [It] relies on a thorough, complete understanding of all input factors for the root cause to be exposed.”
So, what should be used to perform an investigative root cause analysis?
Red X: Pinpointing the True Root Cause
Red X is a rapid, convergent approach designed to isolate the dominant root cause of a problem with unmatched precision by exposing the geometry and/or physics that drive the undesirable outcome.
Unlike Six Sigma’s X-to-Y logic, which begins by analyzing inputs to understand outputs, Red X employs a Y-to-X framework. This approach starts with the problem (the “Y”) and works backward to uncover hidden causes (the “X”) quickly, making it particularly effective in complex or time-sensitive scenarios.
It uses the FACTUAL framework (Focus, Approach, Converge, Test, Understand, Apply, Leverage) to guide teams in resolving challenging problems. While this is technically more steps than the DMAIC model, each has importance:
• Focus: Define the problem and set clear, measurable objectives.
• Approach: Gather data to identify patterns and establish an effective measurement system.
• Converge: Isolate the root cause using systematic elimination and evidence.
• Test: Confirm the root cause with a controlled, statistical test.
• Understand: Explore and define the bounds of the root cause’s influence.
• Apply: Implement corrective actions to control Red X.
• Leverage: Use knowledge gained to apply to other similar challenges.
One of Red X’s defining features is targeted confirmation testing, a step that ensures the suspected Red X is the dominant root cause before implementing corrective actions. Tom explains, “The Red X is confirmed with a statistically valid test to predictively control the specific outcome, turning it on and off like a light switch.”
This method eliminates guesswork, providing concrete evidence that the identified cause directly influences the problem. By validating the solution in this way, teams can confidently implement corrective actions, reducing the risk of rework or unforeseen issues.
Red X thrives in scenarios where problems are sporadic, data is limited, or destructive failures occur. It systematically excludes non-contributing variables, converging on the dominant factor responsible for the failure.
Esther highlights its effectiveness: “Shainin [has different strategies for different types of problems], which makes Red X invaluable when Six Sigma’s reliance on abundant data falls short.”
For instance, in cases of destructive testing and destructive failures where reproducing the failure is costly, impractical, or not yet possible, the Red X approach isolates the critical variables without the need for extensive data collection. This adaptability ensures that Red X delivers results even in the most challenging manufacturing environments.
By pairing its focused approach with rigorous confirmation testing, Red X provides unparalleled speed and accuracy in identifying and resolving root causes.
To dive deeper into this methodology, explore our resources on Red X and the steps of the Red X framework.
How Red X and Six Sigma Work Together
When combined, Red X and Six Sigma offer a comprehensive approach to problem-solving:
1. Rapid Root Cause Identification: When time is of the essence, Red X isolates the primary drivers of a problem quickly. This allows the team to not only identify the cause but also determine its bounds and implement controls to the process that can then be maintained with DMAIC work if production ever yields undesired variation.
2. Validated Solutions: Red X’s confirmation testing ensures solutions are based on fact, allowing Six Sigma to refine and standardize them.
3. Broader Problem Coverage: Red X addresses hidden and sporadic issues, while Six Sigma optimizes well-defined processes for sustained improvements.
As Jay explains, “Red X works well in the Define, Measure, and Analyze phases to generate and confirm causes, while Six Sigma is best suited for the Improve and Control phases to refine and apply corrective actions.”
Case Summary: Aerospace Success with Red X and Six Sigma
In an aerospace sand casting foundry, Six Sigma and Red X were deployed together. SPC (Statistical Process Control) was used to monitor and adjust sand quality, ensuring consistent input. Red X was then applied to uncover unexpected factors like heat transfer and mold geometry, which caused sporadic casting defects. The combined approach led to a significant reduction in scrap and rework, saving time and costs.
The Power of a Complementary Pair
Red X and Six Sigma each bring unique strengths to the problem-solving process, making them a formidable combination for tackling complex challenges. Red X specializes in rapidly isolating root causes through a convergent approach, while Six Sigma drives incremental improvements through variation reduction. This interplay between speed and process control creates a more efficient and effective problem-solving framework.
If you only have a hammer...
Esther captures the essence of this partnership: “If I have a toolbox and only a hammer in it, then it will be difficult to drill a hole. The combination of many methods makes the best problem solvers.” By integrating Red X and Six Sigma, organizations can address problems that span a wide spectrum—from sporadic issues with hidden root causes to process inefficiencies requiring detailed analysis and control.
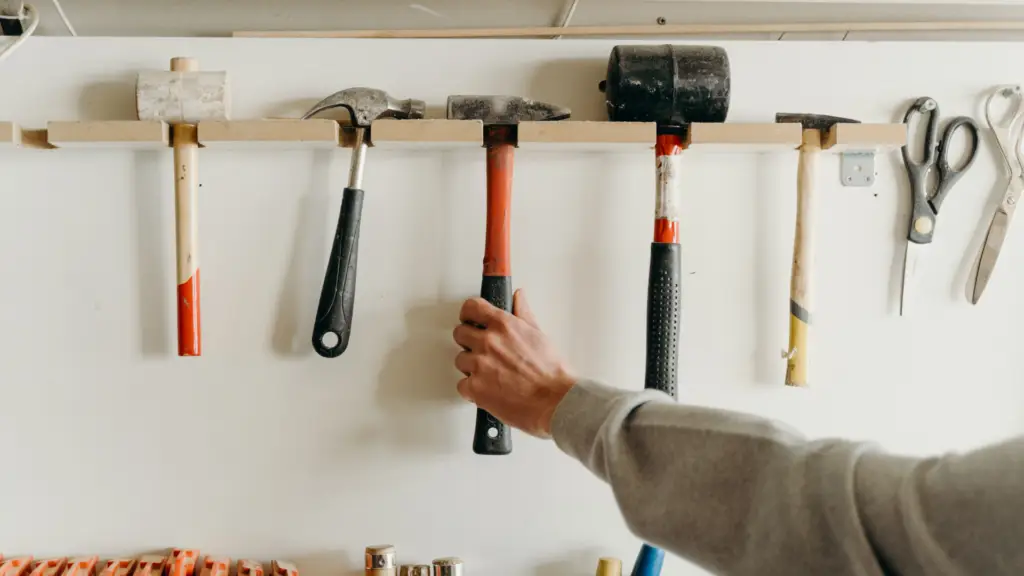
Resolve and then Sustain
Tom highlights how this dual approach accelerates results: “Red X exposes troublesome causes quickly, while Six Sigma validates and sustains the improvements.” Red X’s focus on confirmation testing ensures that root causes are clearly identified and resolved, reducing the risk of missteps. Six Sigma builds on these validated insights to optimize processes and embed solutions into standard operating procedures.
A Balanced Toolkit
What makes this combination so impactful is its flexibility. Red X thrives when traditional data-driven approaches fall short, such as in scenarios with limited information or rare defects. Six Sigma excels in environments where variation needs to be reduced, and long-term improvements are the goal. Together, they provide a balanced toolkit that adapts to the unique demands of each problem.
Tom concludes, “The complimentary toolset of Red X and Six Sigma is essential to competitiveness in the manufacturing world. There is no faster path to true root cause in complex products, systems and processes than Red X. Red X methods will quickly expose the troublesome causes so they can be controlled effectively.”
By embracing both methodologies, companies can ensure that they not only solve the problem at hand but also create a foundation for sustained operational excellence. This pairing enables teams to tackle challenges confidently and efficiently, delivering measurable improvements in quality, efficiency, and financial outcomes.
Complements not Competitors
Red X and Six Sigma are not competing methodologies—they are complementary solutions that, when combined, enhance problem-solving capabilities and deliver measurable results. Whether isolating a hidden defect or refining a complex process, these tools provide a roadmap to operational excellence. By leveraging the best of both approaches, companies can build resilient systems, improve efficiency, and maintain a competitive edge.
Ready to learn more about Red X Problem Solving? Read more here.