Modernizing Product Development
The tools that helped us improve product designs and manufacturing processes since the 1970s are holding us back from reaching the expectations of today.
Traditional techniques, like Failure Mode and Effects Analysis (FMEA), have become outdated. While FMEA has significantly contributed to quality improvements – transforming defect measurement from defects per hundred to defects per million – it remains a method that often focuses on an impractically exhaustive list of potential failure modes.
Introducing Resilient Engineering
Resilient Engineering shifts the focus from identifying endless possible failures to a finite list of critical functions. By converting these critical functions into a manageable list of features, properties, and process parameters, this approach ensures that what must go right, indeed, goes right. Unlike FMEA, which can require extensive experience and knowledge of potential failures, Resilient Engineering operates effectively even without a deep history of prior failures.
The Resilient Engineering Process
Resilient Engineering is structured into three phases: Design Risk Mitigation, Manufacturing Risk Mitigation, and Warranty Risk Mitigation (Figure #1). These phases can be applied independently or collectively, based on the project’s timing and needs. Figure 2 shows a closer look at each phase.
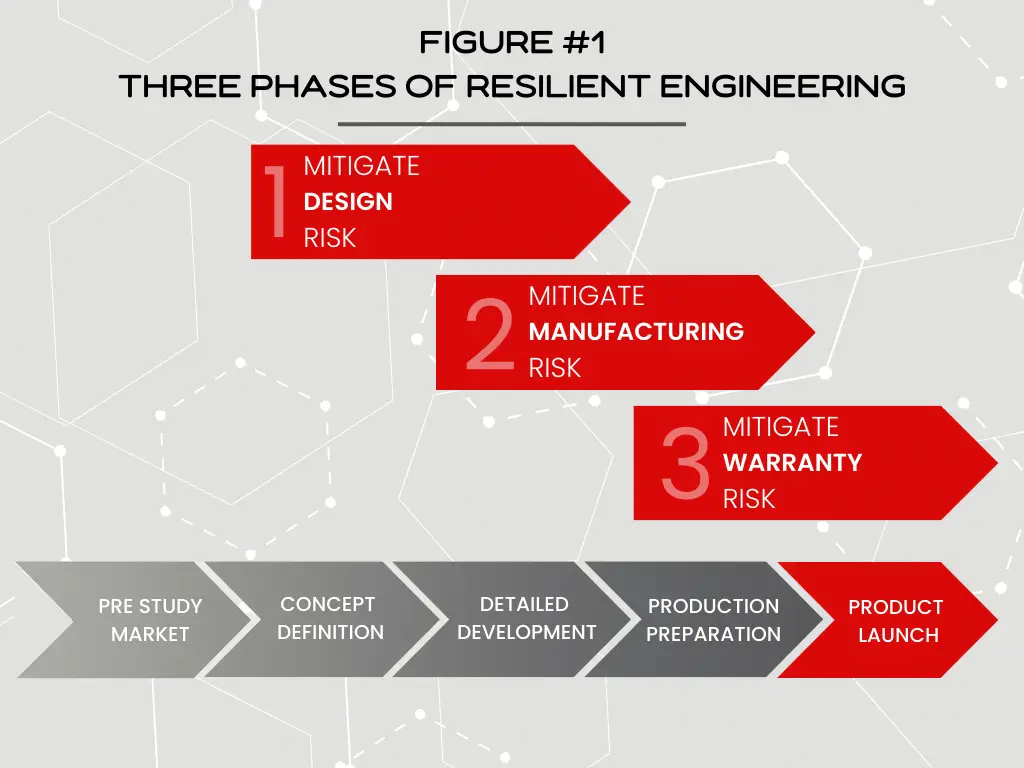
- Design Risk Mitigation: This phase starts with a Focus Risk Priority Pareto, which prioritizes risks based on severity, changes in requirements, and experience. This method overcomes the often inconsistent and guess-based ratings of traditional FMEA by providing a more reliable risk assessment.
- Manufacturing Risk Mitigation: During the Functional Analysis step, high-risk functions are linked to critical input features, properties, and process parameters. Through a patented process, inputs are checked for conflicts with outputs and other inputs. The subsequent Linkage Matrix step condenses this work and assesses measurement system and tolerance capability.
- Warranty Risk Mitigation: The final step, Conceptualized Failure Mode Testing, confirms critical relationships and establishes realistic input tolerances. This is achieved through simulations, physical lab tests, and Overstress Probe Testing™.
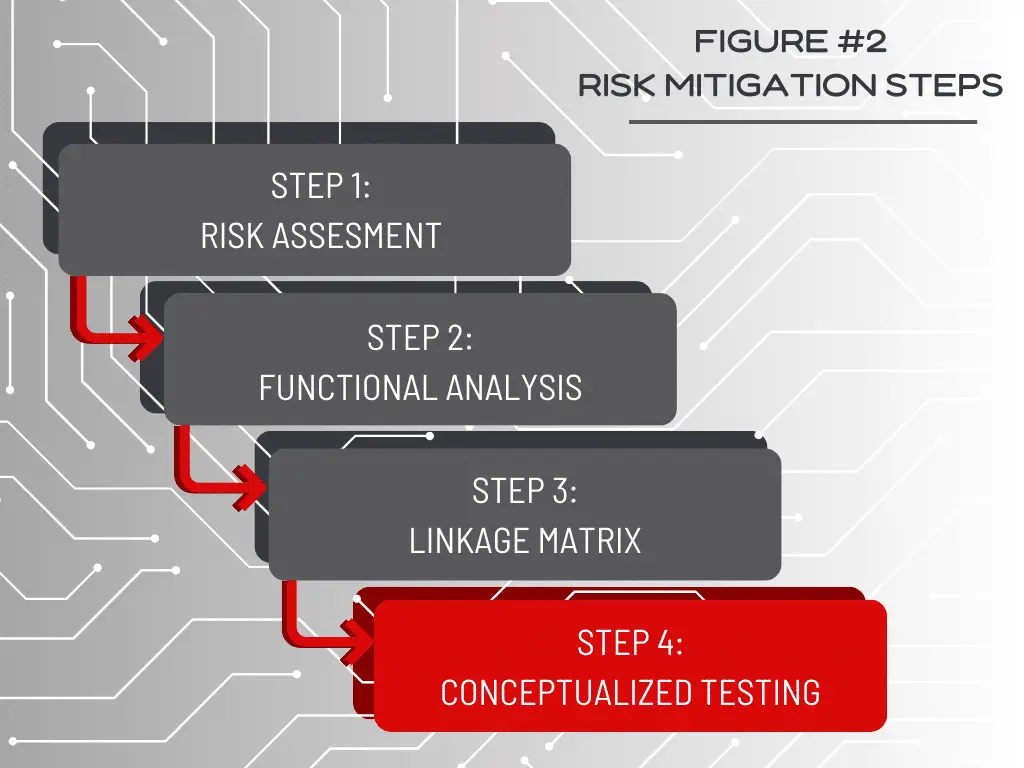
Why Choose Resilient Engineering?
Resilient Engineering integrates seamlessly with existing product development and launch processes. Its laser-focused approach addresses the high-risk areas of a design or process, ensuring the critical functions are executed flawlessly. By concentrating on what must go right, rather than an infinite number of things that could go wrong, Resilient Engineering enables safer and faster product development, even in areas without extensive experience or application history.
Launch your Innovation
Imagine launching a product designed to perform at its best from day one, meeting customer expectations and aiming to set a new standard in your industry. With Resilient Engineering, you have the tools to enhance the reliability of your critical functions, reduce the stress of potential failures, and gain greater confidence in the robustness and reliability of your design.
Contact our team today to see if Resilient Engineering is a good fit for your upcoming product launch.