In the current manufacturing and engineering environment, companies have complex problems triggering issues like scrap, non-scheduled overtime, poor product performance, and warranty claims, resulting in heavy losses and impacting bottom lines.
Companies may try to solve these complex problems with traditional Root Cause Analysis methodologies, but often the expected results fall short.
The most critical problems are those that ‘have always been there’ and people in these organizations have just learned to live with them. The good news is they don’t have to.
The Typical Problem Solving Approach
Most problem solving approaches involve finding the root cause prior to selecting a solution. This allows for the corrective actions to be well targeted with a greater likelihood of fixing the problem. When the root cause of the problem is known, this step is quite simple; just describe it in concise, clear terms so all team members can understand it. The challenge is when the root cause is not known. It is hidden from the team members and thus the corrective action path is unclear.
When the root cause is not known, a method is needed to find it. There are a variety of methods which try to brainstorm a list of potential causes and then arrange them into a diagram. Often the real root cause is a surprise and does not even make the list, or the list is too long and there is no structured way to narrow it down efficiently.
Solve complex problems - permanently.
There is a unique method that stands out from other approaches. It tackles complex problems effectively, delivering results that significantly enhance a company’s performance and outcomes.
This method is known as Red X Problem Solving.
What is Red X Problem Solving?
The Red X Problem Solving method is a structured approach to solving complex problems, quickly and efficiently finding the Root Cause (Red X).
WHAT’S DIFFERENT ABOUT RED X PROBLEM SOLVING?
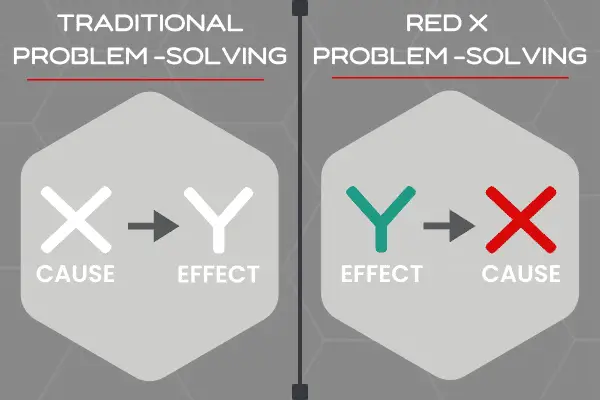
One of the main differences that makes this method for Root Cause Analysis strong is that the investigation goes “backwards” from Y, (Output, known as the Green Y) to X (Inputs). This is opposite to the traditional way of thinking from X (Inputs) to Y (Output) and is known as ‘Y to X thinking’.
In the context of this methodology, the term, “Red X,” refers to the most critical and significant root cause of a problem. It represents the key factor (“Red X”) that, if addressed and resolved, will have the greatest impact on the measured output (“Green Y”), solving the problem and improving the process or product.
In other words, you can solve the problem by simply controlling or eliminating the Red X. This provides an elevated level of efficiency in the problem solving process as you won’t work on solving everything, only the major contributor to the problem.
Note: The Red X can be either a single factor, or a combination of several (also known as an interaction).
“Talk to the Parts”
Identifying the Red X is a crucial step in the problem-solving process as it helps to focus efforts and resources on tackling the most impactful issue. It does this by using statistical tools and techniques, in a convergent investigation following an elimination process based on evidence gathered by what Dorian Shainin describes as, “Talking to the Parts”.
What does it mean to, ‘talk to the parts?’
“Talk to the parts” means to examine physical components to gather objective information. This approach reveals the true performance and issues of the parts, providing honest feedback. It focuses on understanding the actual behavior of the parts rather than relying solely on theoretical explanations from engineers.
Following this approach, teams can make targeted improvements that lead to significant positive outcomes and prevent similar problems from occurring in the future.
This method is used successfully by businesses across many industries, including automotive, aerospace, medical and electronics, independent of the manufacturing process and product type.
Using Red X Problem Solving in Your Organization
How can your company apply and benefit from Red X Problem Solving?
Shainin offers two different options:
• Training programs: Shainin supports the process of selecting candidates to send to a class, followed by project coaching sessions with a Shainin consultant. Through coaching, teams receive dedicated support in getting the expected results on their project work. At the end, the company will benefit from having problems solved with the project work, and certified people who are knowledgeable in using Red X Problem Solving Methodology.
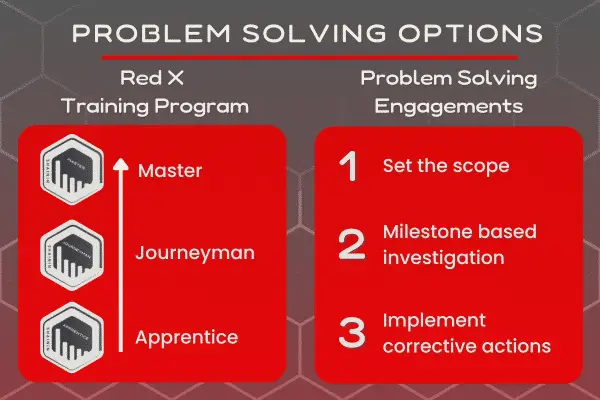
• Problem Solving Engagements: Shainin works with the company to define a working plan and oversee leading the investigation in their facility. Working in milestones or steps from the initial information analysis up to the definition of the Red X, the problem is confirmed with statistical tools and options are then proposed for effective corrective actions.
The option a company chooses often depends on timeline, budget, and internal resources.
To speak with a representative about implementing Red X® Methodology in your organization, please follow this link.
About the Author
Sergio Lizarraga
Sergio Lizarraga is the General Manager of Shainin Mexico and Technical Director for Latin America. He has been using Shainin for more than 25 years, in a variety of manufacturing environments like automotive, electronics, foundry, and medical products, among others. Sergio has trained teams in Mexico, the USA, Argentina, Spain, Brazil, and Portugal in Red X Problem Solving Methodology.