Not every problem solving methodology is right for every problem. And as we continue our series on Problem Solving, it is crucial to emphasize the importance of aligning problem-solving projects with company goals, and learning which problem-solving methodologies are best in certain situations or for certain groups.
In our previous articles (which you can see here and here), we discussed how having a clear understanding of company objectives can help guide the selection of problem-solving tools and methodologies and may even guide you toward one methodology over another. However, it is important to understand that it is not enough to rely on just one method for all your problem-solving needs; in fact, embracing versatility in methodologies can greatly maximize your problem-solving potential and lead to more effective and efficient solutions.
This is especially true in manufacturing facilities, where complex problems require multifaceted approaches and a high degree of flexibility. In this article, we will delve deeper into the significance of utilizing multiple problem-solving methodologies and how doing so can benefit your company’s strategic goals.
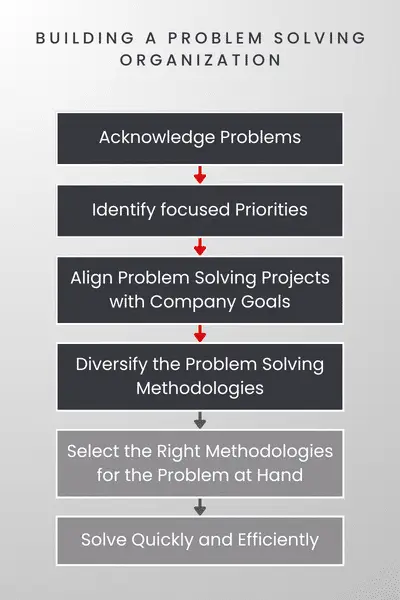
The Power of Diverse Problem-Solving Methodologies
Embracing a broad spectrum of problem-solving methodologies is akin to assembling a versatile toolkit. Each tool—or in this case, each methodology—offers a unique advantage which allows an organization the ability to tailor their approach to each unique challenge presented, particularly in a dynamic environment such as manufacturing.
With ever-evolving technology, our methods must also evolve not only to stay close to the cutting edge but also to help retain and enhance our team. By embracing a diverse set of problem-solving methods, an organization fosters an environment that encourages continuous learning.
Rather than adhering rigidly to one approach, teams are encouraged to explore different methods and adapt their strategies based on the nature of the problem at hand. This flexibility not only enhances problem-solving effectiveness but also fosters a culture of resilience and adaptability in the face of uncertainty.
With the development of a culture of resilience and adaptability, an organization has an unmatched competitive advantage. They have organizational resilience not reliant on any one component.
Why Having More Than One Method Matters
In problem-solving, the allure of a familiar method can be the siren in the distance, compelling you toward a bad outcome. In this case, the “familiar” often overshadows the potential for innovative solutions, leading to cognitive biases that stymie creativity and efficiency. Such biases, deeply ingrained in our decision-making processes, can cause teams to repeatedly gravitate towards the same methodologies, neglecting the breadth of tools at their disposal.
“If the only tool you have is a hammer, you tend to see every problem as a nail.”
Abraham Maslow
The problem is that this habitual reliance on a singular, comfortable approach not only limits the scope of potential solutions, but also amplifies the risk associated with unforeseen challenges. So, by embracing a diverse arsenal of problem-solving methodologies, teams can transcend these cognitive biases, approaching problems from a multitude of perspectives and, thereby, uncovering solutions that might have otherwise remained obscured.
Still, the importance of methodological diversity extends beyond the mitigation of cognitive biases; it is a cornerstone of operational resilience. In a volatile landscape such as manufacturing, where problems can be as unpredictable as they are varied, dependence on a single method of problem-solving is tantamount to navigating a tempest with a single oar. By cultivating familiarity with a spectrum of methodologies, teams equip themselves with the versatility necessary to adapt to and overcome a wide array of challenges, ensuring a robust operational framework capable of withstanding the tests of time and uncertainty.
Selecting the Right Method for the Job
So if we accept that having multiple problem-solving methodologies is the best way to approach problem solving, then selecting the right problem-solving methodology becomes a critical piece of the problem-solving puzzle, and requires a thoughtful analysis of several key factors, each of which plays a critical role in ensuring the effectiveness of the solution developed.
Firstly, understanding the nature and complexity of the problem at hand is paramount.
Simple issues may only need basic troubleshooting, whereas complex, multifaceted problems could benefit from a more elaborate approach, like Red X©, which is renowned for its structured, data-driven methodology aimed at eliminating defects.
But equally important are the available resources and time constraints. For instance, Lean Manufacturing, with its focus on waste reduction and efficiency, is particularly beneficial in scenarios where resource optimization is the highest priority. On the other hand, methodologies that facilitate rapid problem identification and solution development, like Shainin Red X©, may be more appropriate.
In addition to all this, organizational culture and preferences also significantly influence the choice of methodology. A culture steeped in continuous improvement might gravitate towards Kaizen, which emphasizes incremental changes and employee involvement at all levels. Conversely, organizations that thrive on innovation might find Design Thinking, with its user-centered approach, more aligned with their culture. It’s also incredibly important to know when it’s time to shift gears.
Among the methodologies considered, there are a few that are more generalized, “catch-all’s” to keep in your toolbox; for example, Root Cause Analysis stands out for its versatility across a range of problems, focusing on identifying the underlying causes of issues rather than just addressing symptoms. Similarly, for complex challenges that require innovative solutions, Design Thinking can offer a fresh perspective by encouraging creative problem solving through empathy and ideation.
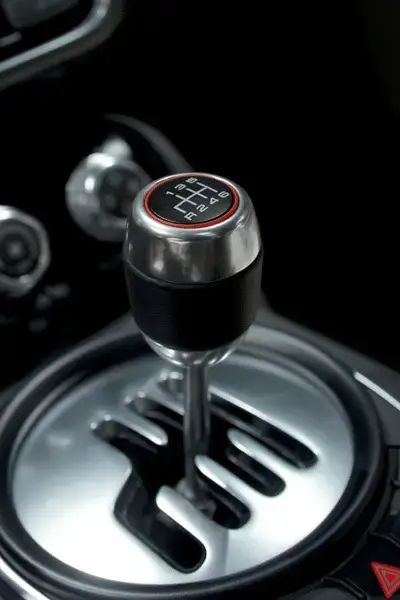
In matching the problem to the appropriate methodology, it’s crucial to weigh these considerations carefully. By aligning the characteristics and requirements of the problem with the strengths of a particular methodology, teams can not only solve problems more efficiently but also foster a culture of adaptability and resilience.
Developing a Versatile Problem-Solving Culture
Cultivating a workplace culture that prioritizes versatility in problem-solving is not just beneficial; it’s essential for staying agile in today’s fast-paced manufacturing environment. But to foster such a culture, it’s imperative that leaders and team members alike champion cross-training and skill development, ensuring that individuals are not just confined to their areas of expertise but are encouraged to learn and apply different problem-solving methodologies.
By diversifying skills within the team, you create a more resilient workforce capable of tackling a wide array of challenges.
Promoting cross-training initiatives can be as straightforward as organizing regular workshops or as immersive as facilitating cross-departmental projects to not only broaden individual skill sets but also enhance team cohesion and understanding.
Encouraging experimentation also plays a critical role in this developmental process. When team members feel safe trying new methods, failure is not seen as a setback but as a steppingstone to innovation and learning.
However, both require a mindset shift across the company to break away from traditional, one-dimensional problem-solving approaches.
Furthermore, fostering an environment of continuous learning propels your team towards expanding their problem-solving capabilities, which can be achieved through mentorship programs, investing in educational resources, or providing access to industry conferences. Such initiatives not only keep your team updated with the latest methodologies but also stimulate a culture of curiosity and continuous improvement.
Methodological Diversity Starts With You
In navigating the intricate landscape of problem-solving within the manufacturing sector, we’ve underscored the indispensable value of methodological diversity.
From enhancing operational resilience to fostering a culture of continuous improvement, the advantages of embracing a wide spectrum of methodologies are clear—and so is the first step: it begins with you—leaders and influencers in the world of manufacturing and engineering.
While the responsibility to drive change and encourage a shift towards diverse problem-solving approaches rests on your shoulders, by championing this cause you not only pave the way for more innovative and effective solutions, but also build a more adaptable and robust operational framework capable of weathering the unpredictability of industry challenges.
So, let this be a challenge to you: Prioritize the growth of a problem-solving culture that celebrates diversity in methodologies and encourage your teams to explore, learn, and apply a broad range of problem-solving tools, ensuring they are well-equipped to tackle the complexities of modern manufacturing challenges. In doing so, you’ll be better positioned to unlock the full potential of your problem-solving capabilities.