Continuous improvement is a cornerstone of success for any organization wanting to stay competitive in today’s dynamic world. To achieve sustained growth and efficiency, companies need to develop a culture of continuous improvement in all areas of their operations. A key strategy to drive a continuous improvement culture is aligning team projects with company goals.
To begin, let’s clarify the meaning of “projects”. For this article, a project is defined as a collaborative enterprise carefully planned to achieve a particular aim. As a problem-solving company, we tend to consider technical problems and the team efforts to resolve them as projects.
Benefits of Connecting Goals & Team Projects
Tying team projects to company goals not only ensures that individual efforts are directed towards the organization’s objectives but also creates a sense of purpose and unity among team members. Team members are more likely to feel a sense of ownership and responsibility for their projects, knowing that their efforts contribute directly to the success of the entire organization.
This alignment promotes a shared vision and fosters a collaborative environment where teams work together towards common goals. This collaboration can also lead to more efficient use of resources and more adaptable teams.
When team members understand how their projects align with the company’s strategic goals, they are more motivated to deliver exceptional results. The sense of purpose instilled by this alignment enhances employee engagement, leading to higher job satisfaction and a more committed workforce.
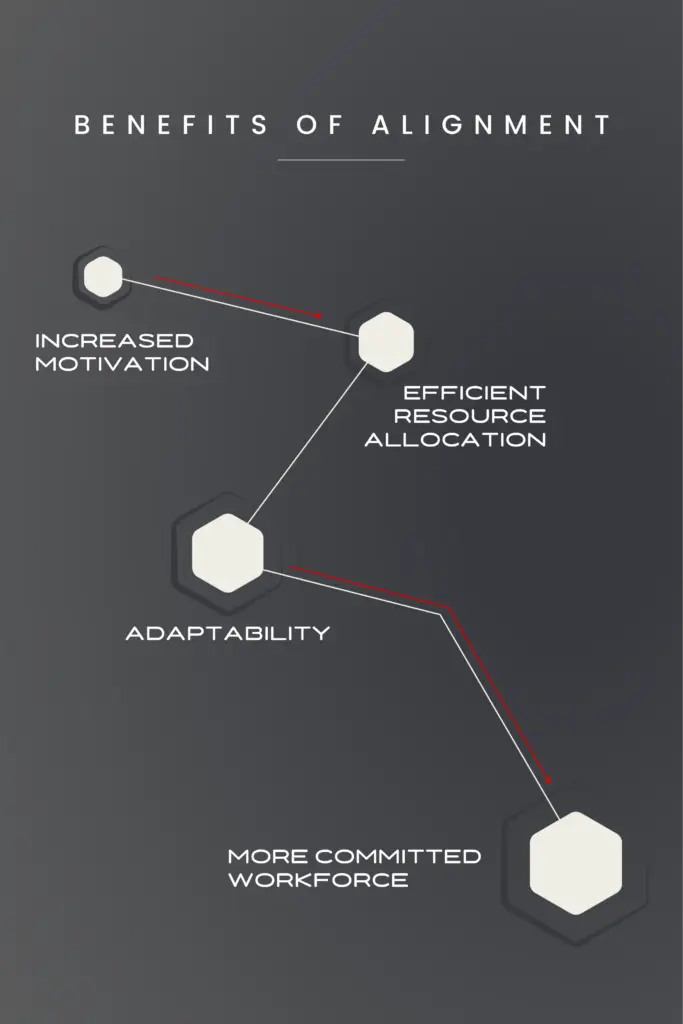
Optimizing Limited Resources
In any company, resources are limited, no matter if we are talking about people or testing equipment. Tying team projects to company goals can ensure that these resources are allocated in the most efficient way. When leadership has taken the time to do this, teams are less likely to work on projects that do not contribute to the overall objectives. This reduces wasted time and effort on activities that are not aligned with the company’s strategic direction and do not contribute to enhancing a company’s bottom line.
Fast-paced Adaptability
In today’s fast-paced business landscape, the ability to quickly adapt is crucial. When team projects are closely tied to company goals, teams can respond more effectively to changes in the external environment. This adaptability is essential for navigating uncertainties and seizing new opportunities as they arise.
Making the Connections
Once a company recognizes the need to tie team projects to the company goals, the next question becomes how to do it on a consistent basis. To succeed in linking the two, leaders must clearly define and communicate the company goals, empower teams to work autonomously, and celebrate achievements.
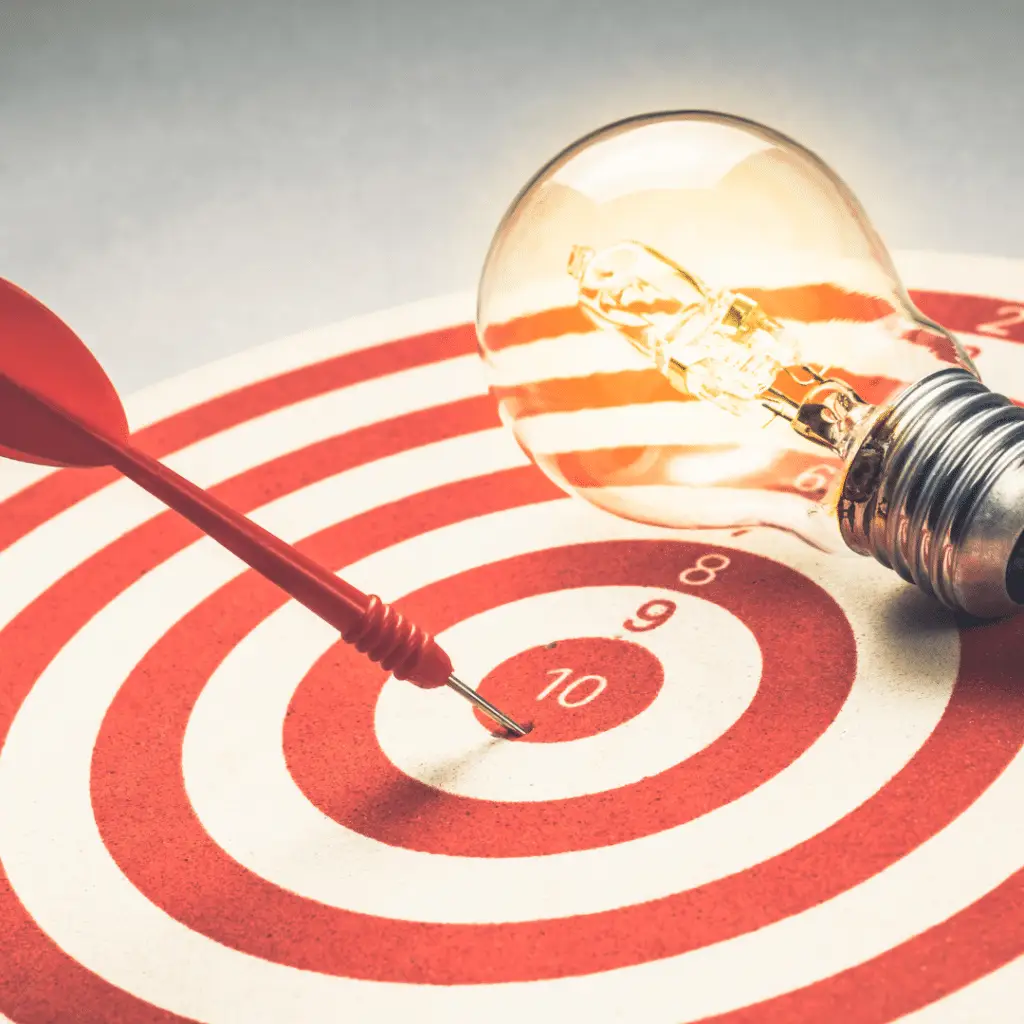
1. Define the Strategic Goals: Before team projects can be aligned with company goals, it is necessary for the organization to have well-defined strategic objectives. These goals should be specific, measurable, achievable, relevant, and time-bound (SMART). This clarity ensures that teams have a clear roadmap to follow.
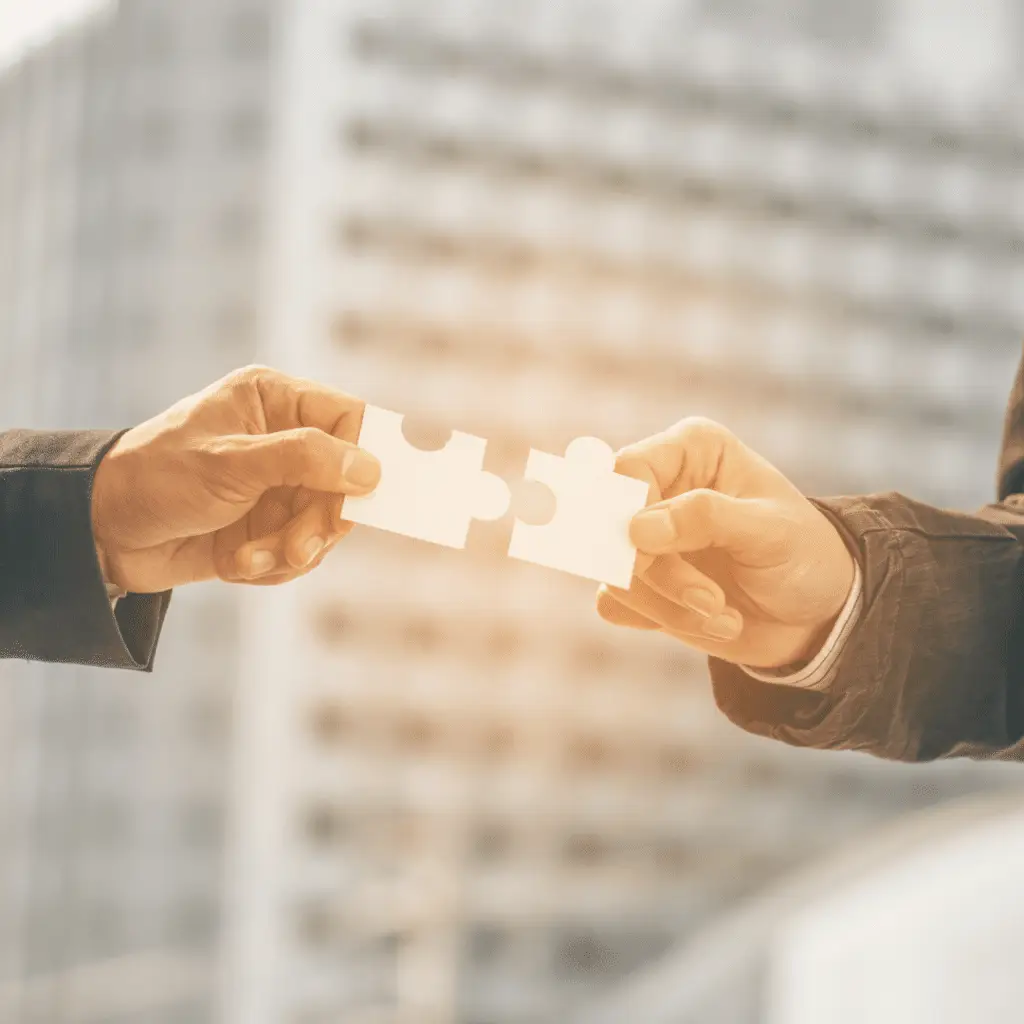
2. Communicate & Connect: Once the company goals are established, effective communication is key. Leaders should ensure that every team member understands the broader vision and how their contributions fit into the larger picture. This can be established by demonstrating how the tangible result of a project directly relates to a specific goal. Regular communication through team meetings, newsletters, and other channels can reinforce this understanding.
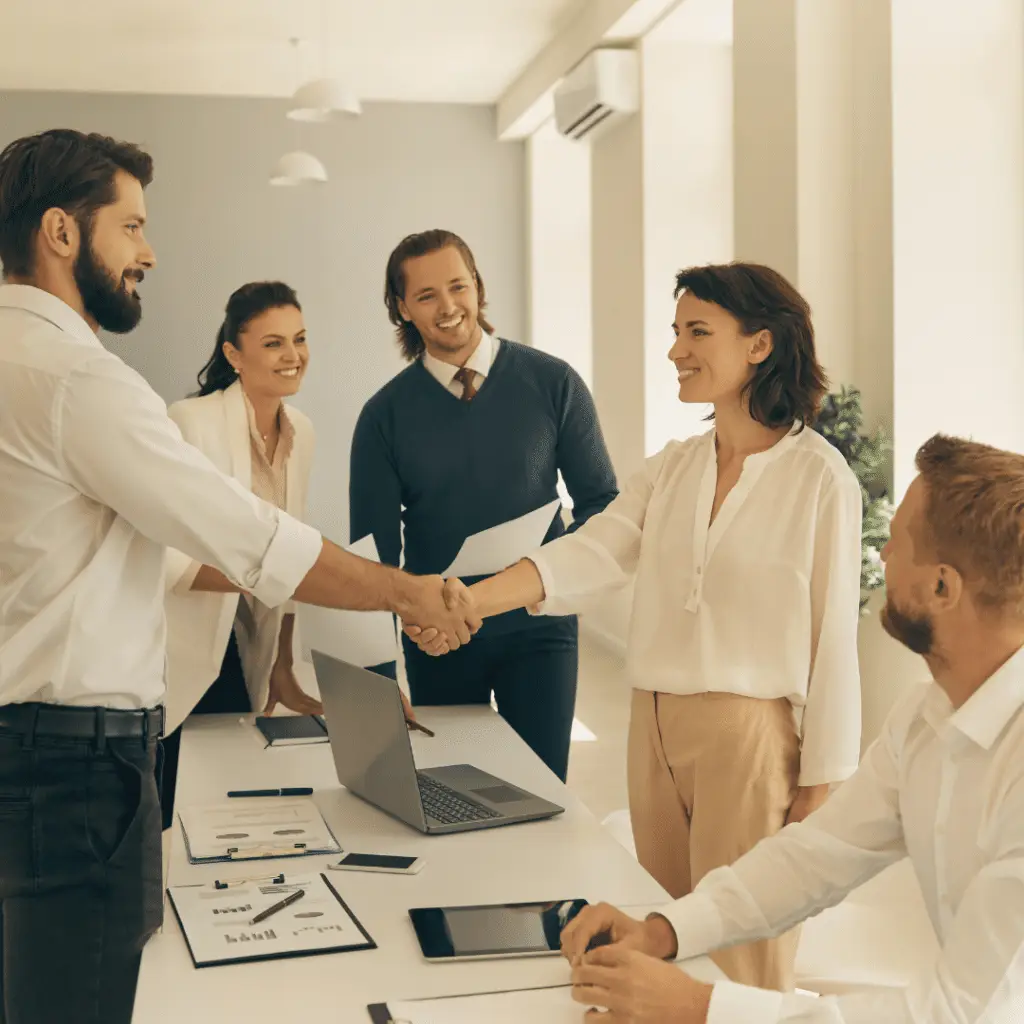
3. Create Team Autonomy & Trust: While alignment is crucial, it’s also essential to give teams the autonomy to devise strategies and solutions that best fit their specific projects. Empowering teams fosters a sense of ownership and encourages innovative thinking. Leaders should provide guidance and support in removing roadblocks while allowing teams the freedom to make decisions within the framework of company goals.
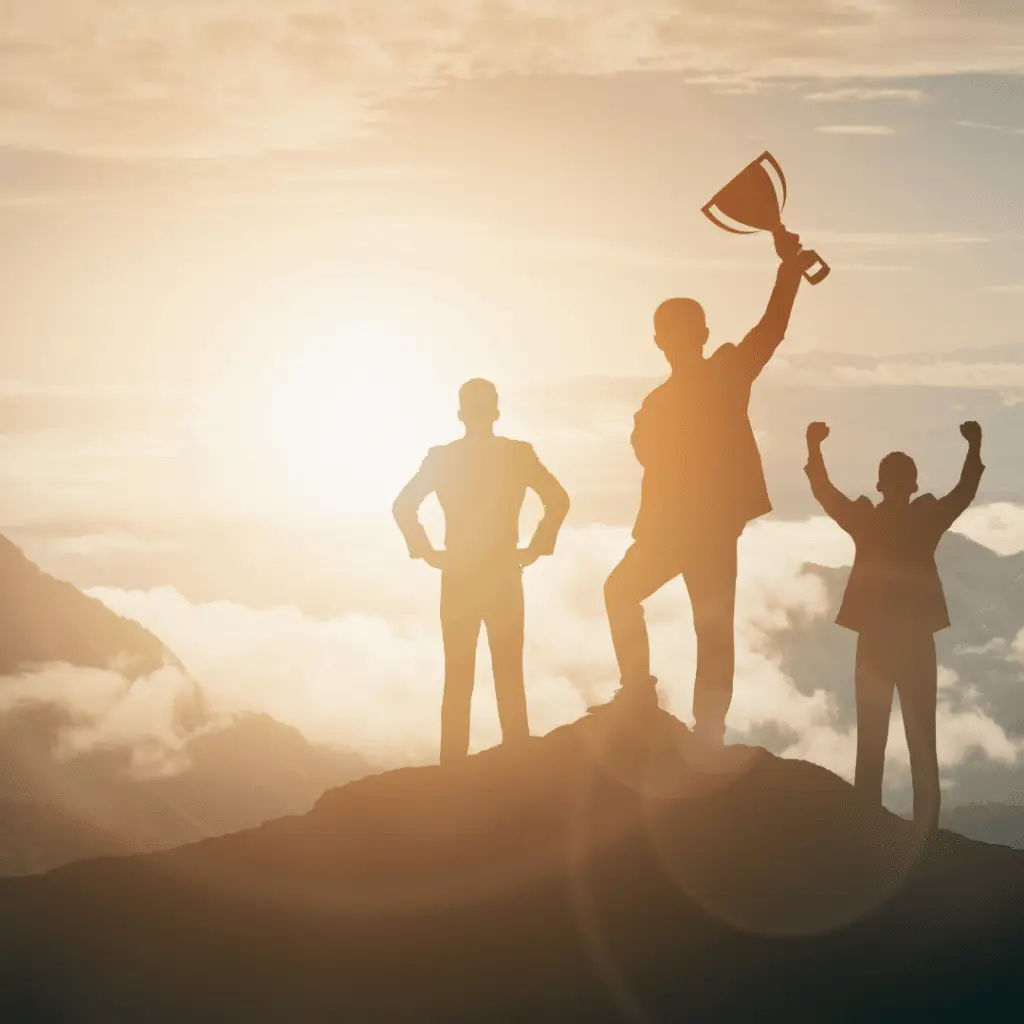
4. Celebrate Successes: An often-overlooked part of the continuous improvement process is celebrating team wins and achievements, but it is critical for continued success. Recognizing and celebrating achievements, both at the team and company levels, reinforces the value of alignment. Whether it’s meeting project milestones or contributing to the achievement of overarching goals, acknowledging successes boosts morale and encourages a positive mindset towards continuous improvement.
Drive Continuous Improvement with Targeted Success
Driving continuous improvement by tying team projects to company goals is a strategic approach that can transform the way your company operates. As part of the focused leadership team, your company’s success is based on your decisions. Integrating a direct tie from your team’s work to the strategic goals of the company is a direct win-win. It not only helps to focus on the right work but also to drive successful and impactful continuous improvement.
It is not just about achieving short-term objectives but building a foundation for long-term growth and excellence.
Need help creating a culture of shared purpose, motivation, and collaboration that leads to improved performance and sustained success? —Just reach out to us and start a conversation. We’re happy to assist you in transforming how your company selects and solves problems so you can solve faster and more efficiently.