About Shainin
Stop Drowning. Start Solving. And Get Really Good At It.
Partner with a team that will get you there
Solving problems shouldn't be what holds you back from delivering For Your customers
Let’s be real. Hearing “we’re going to source another vendor” or “we’re having too many failures” from your stakeholders is never a good place to be.
Because no matter how much your customer likes you,
repeated failures and problems can’t be overlooked.
And that’s where
we come in…
You need different. And we do things differently to get you better results.
We’re Shainin
you solve problems.
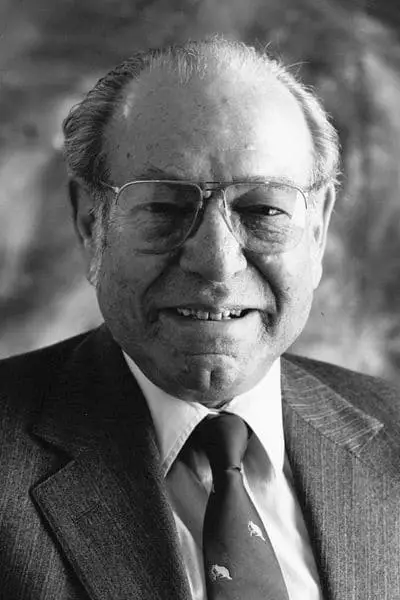
A problem solving company wasn’t originally the goal. But after years of helping companies around the world get better quality products, fewer defects, and higher reliability, Dorian Shainin formalized his methods of helping others into:
Simple & Powerful Problem-solving tools
for any business
No matter
the industry
Over the years,
We’ve helped businesses in multiple industries solve their chronic quality problems and business process disruptions.
Companies like Bosch & Philips have partnered with us to develop problem solving programs to develop their teams into expert problem solvers.
For a team that began as one man, we’re proud to assist companies in transforming how they solve problems to an efficient solving machine with impressive speed.
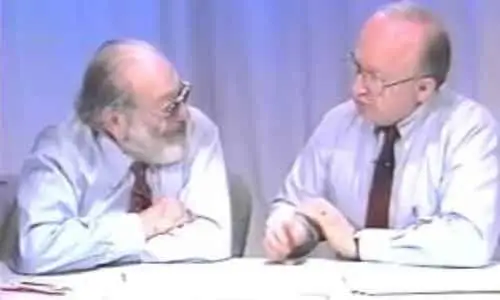
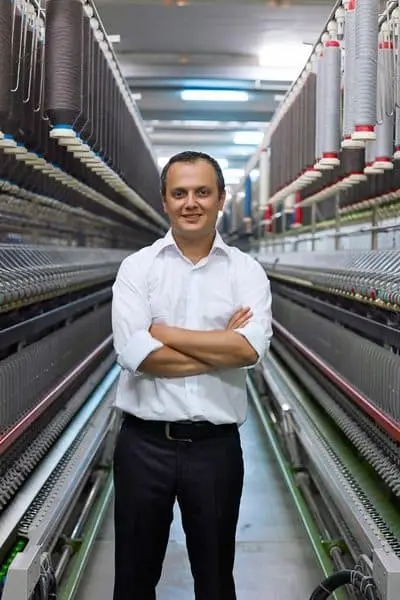
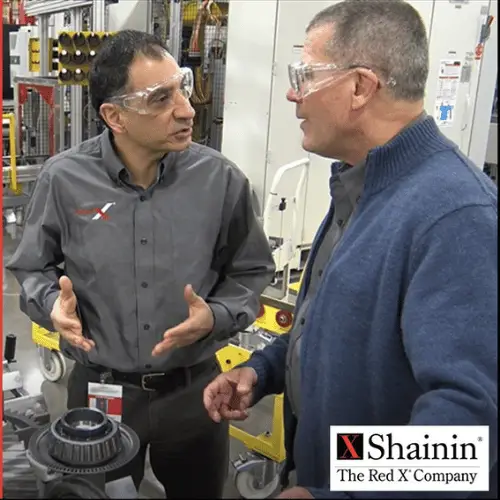
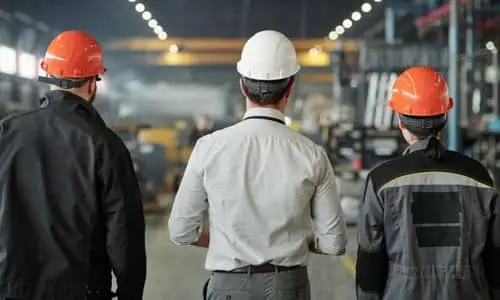
Our Different Approach
Simple in Form
We believe problem solving tools shouldn’t take a masters degree in statistics to use. Our process and tools have been refined & honed to make them approachable for everyone on your team.
Focus
Solving complex problems requires focus. We take time to fully define the problem we’re working on before jumping in. Our main focus is the root of the problem causing your specific pain.
Y to X
You don’t have to know all the causes of variation, just the ones that matter. We start with the outcome and converge to the root cause, not the other way around. It works, and it works fast.
Doing things differently
Focus on what matters
Many companies live with unsolved problems. But they don’t have to. Our client’s challenges wake us up in the morning and sometimes keep us up at night, but we wouldn’t have it any other way.
We believe that every problem is solveable with the right tools and the right team. From decades of innovations to hiring the right team, we feel we’ve got the perfect combination of tools and team to truly transform how organizations solve their most critical problems.
A team of innovators
Making life Easier with innovative methods
The Shainin Team is driven by a need to help solve problems. We work in some of the most complex industries in the world. Combine that with being the go-to problem-solving partner to fortune 100 companies and high-volume manufacturers pushes us to innovate each day to make life easier.
Our team is inspired by the new challenges that our partners bring and is constantly working to create the simple but effective solutions and tools to serve them best.
We get to learn new things and help our clients regain confidence in their operations and teams every day. We think there’s no better way to use our skills than that.
Meet the leaders
Never Out of Reach
Worldwide Resources
We are never out of reach. You have access to our global network of experts who concentrate their knowledge and expertise on the issues that matter to you.
Shainin combines global scale with local focus. In most places, our team will not only speak your language, we will understand your customs and how business gets done.
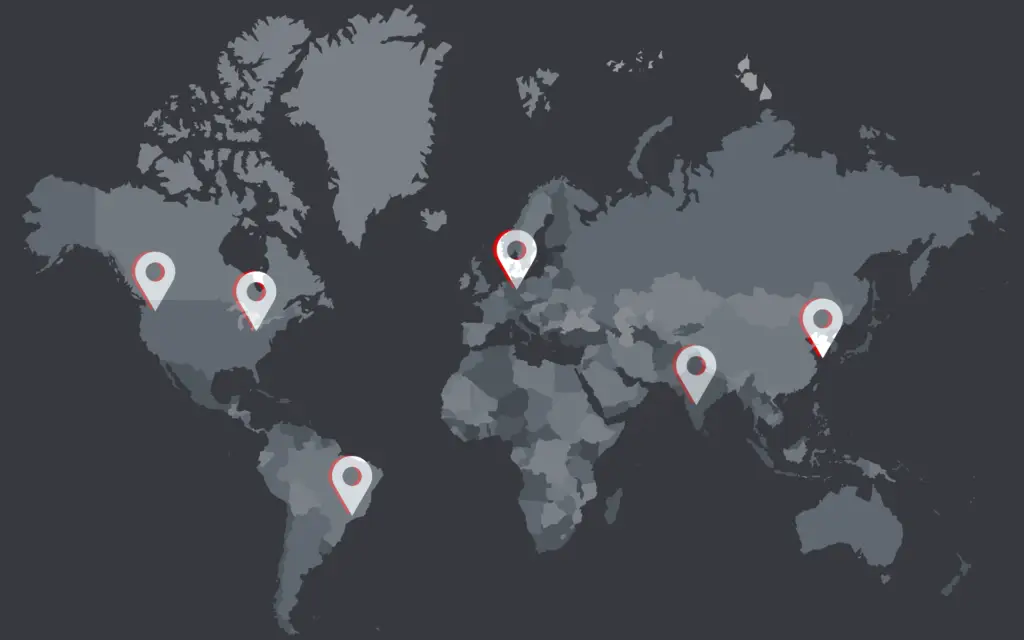
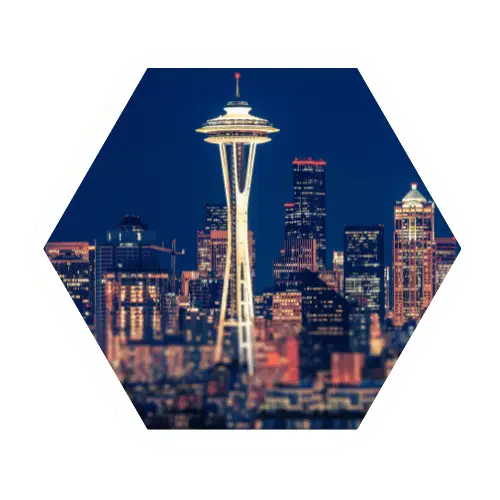
Seattle, Wa - USA
Lorem ipsum dolor sit amet, consectetur adipiscing elit. Ut elit tellus, luctus nec ullamcorper mattis, pulvinar dapibus leo.
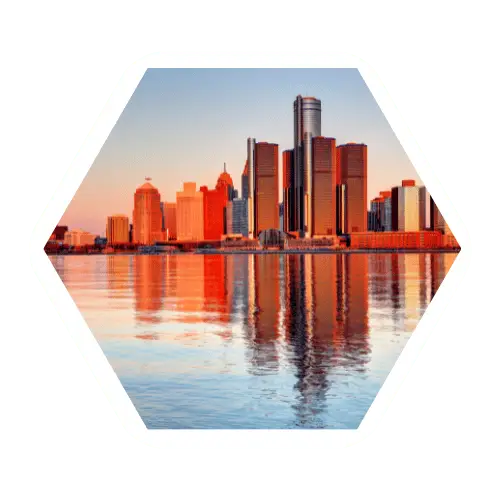
Detroit, MI - USA
Lorem ipsum dolor sit amet, consectetur adipiscing elit. Ut elit tellus, luctus nec ullamcorper mattis, pulvinar dapibus leo.
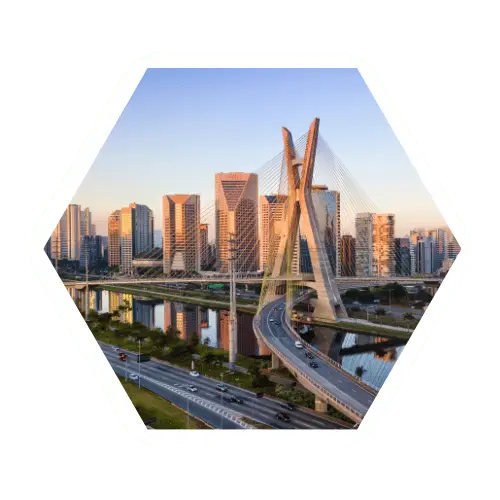
Sao Paulo, Brazil
Lorem ipsum dolor sit amet, consectetur adipiscing elit. Ut elit tellus, luctus nec ullamcorper mattis, pulvinar dapibus leo.
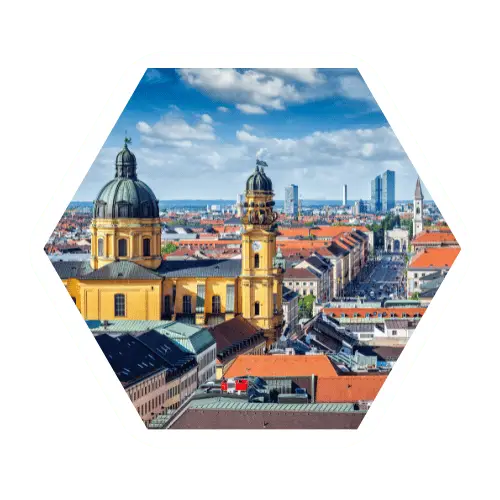
Munich, Germany
Lorem ipsum dolor sit amet, consectetur adipiscing elit. Ut elit tellus, luctus nec ullamcorper mattis, pulvinar dapibus leo.
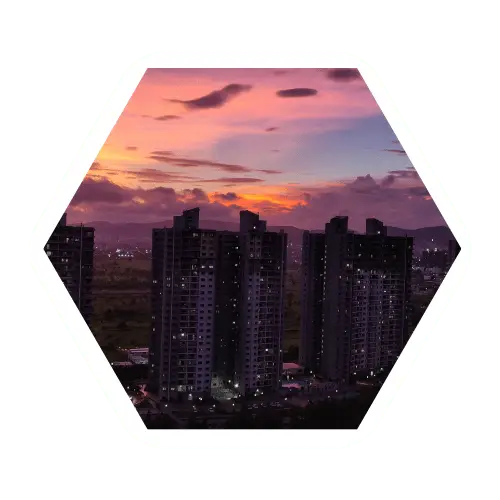
Pune, India
Lorem ipsum dolor sit amet, consectetur adipiscing elit. Ut elit tellus, luctus nec ullamcorper mattis, pulvinar dapibus leo.
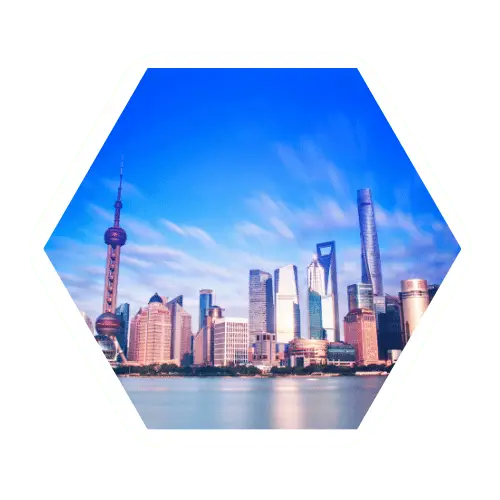
Shanghai, China
Lorem ipsum dolor sit amet, consectetur adipiscing elit. Ut elit tellus, luctus nec ullamcorper mattis, pulvinar dapibus leo.
Complex issues require innovation
Review our Decades of Innovation
After decades of innovation, we’ve developed the ideal combination of statistical rigor and simplified tools to create a transformative problem solving approach.
![]() |
“Talk to the Parts” |
Talking to the parts moves away from speculating about what could be wrong and provides a structured, disciplined approach that gets you to the real culprit in a more efficient manner. | |
CATEGORY: Complex Technical Problem Solving | |
![]() |
Service Monitoring |
Service Monitoring is a method for discovering dangerous failure modes when new products are put into actual service. The purpose for service monitoring is to supplement lab testing in anticipation of environmental stresses that aren’t expected. This can expose serious problems before they impact the customer. | |
Category: Product Development & Reliability | |
![]() |
Red X Principle |
When you have a challenging problem with a hidden source, often the instinct is go through every potential driver of the issue. However, the Red X principle allows you to converge on the single driver that contributes to most of the variation, allowing you to quickly identify and understand the problem. | |
CATEGORY: Complex Technical Problem Solving |
![]() |
Component Search |
Component Search was born from a serious issue with hydraulics in airplanes. This technique isolates components in a system that contribute to variations. It is a highly disciplined, structured approach that allows the user to quickly isolate whether the problem is coming from the assembly process or from the parts, then pinpoints WHICH parts are contributing to the difference. | |
CATEGORY: Complex Technical Problem Solving | |
![]() |
Overstress Probe Testing |
Overstress probe testing is a method Dorian developed to support Grumman in the development of the lunar module in the Apollo program. NASA required the lunar module have a reliability of 99.99%, or 1 failure in 10,000 missions. In the field of reliability, what’s meaningful is the ability to predict reliability with confidence. With overstress probe testing, Dorian could get 90% confidence for 99.99% reliability, which won him the contract. Used in the Apollo program, the lunar module was 100% reliable. In fact, in Apollo 13, the service module exploded, and the command module was damaged. Because the lunar module was so reliable, the astronauts were saved. In short, this testing helps users identify failure modes they wouldn’t otherwise anticipate. | |
CATEGORY: Product Development & Reliability |
![]() |
Tolerance Parallelogram |
The Tolerance Parallelogram is a graphical technique that allows engineers to establish tolerances for the Red X that are related to their customers’ actual experience. Most tolerances established for manufacturing are based on design engineer judgement; however, this technique allows engineers to establish realistic tolerances so that the product performs to customer expectations. | |
CATEGORY: Process Management & Control | |
![]() |
B vs C |
This simple, quick statistical test determines if a new design or method is better than the current one. Completed with extraordinarily small sample sizes, this test can be used to test a potential solution in manufacturing problems. | |
CATEGORY: Confirmation Testing | |
![]() |
Isoplot |
This graphical technique allows engineers to assess the variability of a measurement system. This helps them see key differences as well as determine how much of the variation is due to measurement variation and how much is coming from the parts themselves. | |
CATEGORY: Complex Technical Problem Solving | |
![]() |
Variable Search |
Variable Search allows customers to experiment with more factors without resorting to a fractional factorial. It also allows designed experiments to be completed with more than four factors without confounding. | |
CATEGORY: Complex Technical Problem Solving |
Allows users to identify the specific feature or input that’s driving a ifference, making it a detailed tool for identifying the Red X. It gets the customer to the final answer. CATEGORY: Complex Technical Problem Solving |
![]() |
Rolling Top 5 |
Rolling Top 5 is a system that brings structure and discipline to the leadership role on problem-solving teams. Even better, it magnifies the impact of problem-solving programs, at least doubling the ROI of the program! | |
CATEGORY: Executive Coaching | |
![]() |
Tolerance Ellipse |
The tolerance ellipse allows the user to establish tolerances for two inputs together, called a Red X and a strong pink X. It also allows the user to establish two customer-identified inputs that are important, giving more flexibility in choosing significant inputs. | |
CATEGORY: Process Management & Control |
![]() |
FACTUAL |
Every problem-solving method needs a roadmap. For RedX, FACTUAL functions as the structure for finding and controlling Red Xs, leading the user to the hidden cause of complex technical problems when it matters most. | |
CATEGORY: Complex Technical Problem Solving | |
![]() |
TransaXional Strategies |
Technical problem solving is one thing, but business process problems are another. Technical problems are bound by physics, but business processes aren’t. Our journey to assist customers in business process problem solving started as a single customer challenge, but we found we loved it. This led to the creation of the TransaXional method, a solidified roadmap for solving business process problems. | |
CATEGORY: Business Process Improvement & Optimization | |
![]() |
Function Models |
A function model is a functional base description of a system in order to identify how it really works. This Y to X approach helps users understand how processes actually work, which provides a robust frame for the process that is being perfected. | |
CATEGORY: Product Development & Reliability | |
![]() |
Strategy Diagram |
The Strategy Diagram is a tool for documenting the structure of a system. This allows the problem solver to make choices as to which strategy is going to be most efficient, which helps the user map out exactly where to focus their efforts in terms of testing the system. | |
CATEGORY: Complex Technical Problem Solving |
![]() |
DETAIL |
Every problem solving method needs a roadmap. For TransaXional, DETAIL functions as the structure for solving business process problems, aiding problem solvers in pinpointing the hidden causes of these serious problems. | |
CATEGORY: Business Process Improvement & Optimization | |
![]() |
Resilient Engineering |
This system is ideal for new process and product development. It provides users with a finite number of functions that must go right in order for the system to work, which helps companies achieve a trouble-free product launch. | |
CATEGORY: Product Development & Reliability | |
![]() |
NTF or No Trouble Found |
This problem-solving method is designed to combat those problems where the answer has previously been “NTF,” or no trouble found. It allows users to address challenging problems when it appears there is no issue present. | |
CATEGORY: Product Development & Reliability | |
![]() |
Corrective Action Trees |
This is a tried-and-true method of documenting the structured innovation required when the Red X turns out to be outside of the manufacturer’s control. When outside energy is causing failure, the corrective action tree finds what options users have to make up for issues that are present. | |
CATEGORY: Complex Technical Problem Solving |
- 1947-1956
- 1957-1966
- 1967-1976
- 1977-1986
- 1987-1996
- 1997-2006
- 2007-Present
![]() |
“Talk to the Parts” |
Talking to the parts moves away from speculating about what could be wrong and provides a structured, disciplined approach that gets you to the real culprit in a more efficient manner. | |
CATEGORY: Complex Technical Problem Solving | |
![]() |
Service Monitoring |
Service Monitoring is a method for discovering dangerous failure modes when new products are put into actual service. The purpose for service monitoring is to supplement lab testing in anticipation of environmental stresses that aren’t expected. This can expose serious problems before they impact the customer. | |
Category: Product Development & Reliability | |
![]() |
Red X Principle |
When you have a challenging problem with a hidden source, often the instinct is go through every potential driver of the issue. However, the Red X principle allows you to converge on the single driver that contributes to most of the variation, allowing you to quickly identify and understand the problem. | |
CATEGORY: Complex Technical Problem Solving |
![]() |
Component Search |
Component Search was born from a serious issue with hydraulics in airplanes. This technique isolates components in a system that contribute to variations. It is a highly disciplined, structured approach that allows the user to quickly isolate whether the problem is coming from the assembly process or from the parts, then pinpoints WHICH parts are contributing to the difference. | |
CATEGORY: Complex Technical Problem Solving | |
![]() |
Overstress Probe Testing |
Overstress probe testing is a method Dorian developed to support Grumman in the development of the lunar module in the Apollo program. NASA required the lunar module have a reliability of 99.99%, or 1 failure in 10,000 missions. In the field of reliability, what’s meaningful is the ability to predict reliability with confidence. With overstress probe testing, Dorian could get 90% confidence for 99.99% reliability, which won him the contract. Used in the Apollo program, the lunar module was 100% reliable. In fact, in Apollo 13, the service module exploded, and the command module was damaged. Because the lunar module was so reliable, the astronauts were saved. In short, this testing helps users identify failure modes they wouldn’t otherwise anticipate. | |
CATEGORY: Product Development & Reliability |
![]() |
Tolerance Parallelogram |
The Tolerance Parallelogram is a graphical technique that allows engineers to establish tolerances for the Red X that are related to their customers’ actual experience. Most tolerances established for manufacturing are based on design engineer judgement; however, this technique allows engineers to establish realistic tolerances so that the product performs to customer expectations. | |
CATEGORY: Process Management & Control | |
![]() |
B vs C |
This simple, quick statistical test determines if a new design or method is better than the current one. Completed with extraordinarily small sample sizes, this test can be used to test a potential solution in manufacturing problems. | |
CATEGORY: Confirmation Testing | |
![]() |
Isoplot |
This graphical technique allows engineers to assess the variability of a measurement system. This helps them see key differences as well as determine how much of the variation is due to measurement variation and how much is coming from the parts themselves. | |
CATEGORY: Complex Technical Problem Solving | |
![]() |
Variable Search |
Variable Search allows customers to experiment with more factors without resorting to a fractional factorial. It also allows designed experiments to be completed with more than four factors without confounding. | |
CATEGORY: Complex Technical Problem Solving |
![]() |
Paired Comparison |
A paired comparison allows users to identify the specific feature or input that’s driving a difference, making it a detailed tool for identifying the Red X. In short, it helps pinpoint the hidden cause of the problem quickly and easily. |
|
CATEGORY: Complex Technical Problem Solving |
![]() |
Rolling Top 5 |
Rolling Top 5 is a system that brings structure and discipline to the leadership role on problem-solving teams. Even better, it magnifies the impact of problem-solving programs, at least doubling the ROI of the program! | |
CATEGORY: Executive Coaching | |
![]() |
Tolerance Ellipse |
The tolerance ellipse allows the user to establish tolerances for two inputs together, called a Red X and a strong pink X. It also allows the user to establish two customer-identified inputs that are important, giving more flexibility in choosing significant inputs. | |
CATEGORY: Process Management & Control |
![]() |
FACTUAL |
Every problem-solving method needs a roadmap. For RedX, FACTUAL functions as the structure for finding and controlling Red Xs, leading the user to the hidden cause of complex technical problems when it matters most. | |
CATEGORY: Complex Technical Problem Solving | |
![]() |
TransaXional Strategies |
Technical problem solving is one thing, but business process problems are another. Technical problems are bound by physics, but business processes aren’t. Our journey to assist customers in business process problem solving started as a single customer challenge, but we found we loved it. This led to the creation of the TransaXional method, a solidified roadmap for solving business process problems. | |
CATEGORY: Business Process Improvement & Optimization | |
![]() |
Function Models |
A function model is a functional base description of a system in order to identify how it really works. This Y to X approach helps users understand how processes actually work, which provides a robust frame for the process that is being perfected. | |
CATEGORY: Product Development & Reliability | |
![]() |
Strategy Diagram |
The Strategy Diagram is a tool for documenting the structure of a system. This allows the problem solver to make choices as to which strategy is going to be most efficient, which helps the user map out exactly where to focus their efforts in terms of testing the system. | |
CATEGORY: Complex Technical Problem Solving |
![]() |
DETAIL |
Every problem solving method needs a roadmap. For TransaXional, DETAIL functions as the structure for solving business process problems, aiding problem solvers in pinpointing the hidden causes of these serious problems. | |
CATEGORY: Business Process Improvement & Optimization | |
![]() |
Resilient Engineering |
This system is ideal for new process and product development. It provides users with a finite number of functions that must go right in order for the system to work, which helps companies achieve a trouble-free product launch. | |
CATEGORY: Product Development & Reliability | |
![]() |
NTF or No Trouble Found |
This problem-solving method is designed to combat those problems where the answer has previously been “NTF,” or no trouble found. It allows users to address challenging problems when it appears there is no issue present. | |
CATEGORY: Product Development & Reliability | |
![]() |
Corrective Action Trees |
This is a tried-and-true method of documenting the structured innovation required when the Red X turns out to be outside of the manufacturer’s control. When outside energy is causing failure, the corrective action tree finds what options users have to make up for issues that are present. | |
CATEGORY: Complex Technical Problem Solving |
Innovative structure & refined simplicity that yields speed to resolution
Let our team of dedicated problem solvers help resolve your most impactful issues. Contact us today to team up!